Innovative Micro Technology (IMT) Introduces Getter Deposition Services
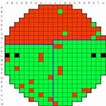
Santa Barbara, CA - Innovative Micro Technology recently announced it has begun offering getter deposition services for wafer-level packaging of MEMS and other devices that require hard vacuum for device performance. In exhaustive testing, IMT has demonstrated vacuum levels equal to or surpassing other established getter deposition services. Using IMT's proprietary getter (patent pending), IMT has routinely achieved vacuum levels below 10 mTorr in production of inorganic devices for such applications as IR emission and sensing and for resonant oscillators in biological and chemical hazard detection applications.
IMT's getter deposition services are performed on 150mm or smaller wafers in IMT's Class 100 cleanroom in Santa Barbara, California with fast turnaround of 3-4 weeks for patterned wafers. Faster turnaround is available on request. Shadow masking services are also available. Customers are encouraged to call for price quotations and delivery.
IMT CEO, John Foster commented, "We see this addition to our MEMS manufacturing services as fulfilling an industry-wide need for fast-turnaround, cost-effective deposition of high-quality getters to enable wafer-level packaging of a wide range of devices that require a vacuum environment. Our getter has been proven to be equal to or better than the industry standard materials available today."
IMT also offers a full suite of MEMS design, prototyping, and production manufacturing services to fabless and fab-light companies in our 30,000 square foot Class 100 fab, the largest and best-equipped independent MEMS fab in the world. Services include: Basic device design and design for manufacturability
- Extensive high-volume manufacturing experience, including SQC/SPC
- 6" wafer efficiency
- 30,000 sq. ft. Class 100, fully automated clean room/fab with superior tool set for all aspects of wafer processing
- Sub-micron photolithography to 0.35um
- Wafer-level bonding (glass frit, eutectics, anodic, fusion, polymer) for device encapsulation (vacuum, atmospheric and partial pressures) and microfluidic construction * Getter deposition for vacuum wafer-level packaging (firing temperature 400C)
- Deep reactive ion etching (DRIE)
- Electroplating of Au, Cu, Ni, In, NiFe, and other alloys
- Chemical-mechanical polishing (CMP)
- Extensive non-CMOS materials flexibility in deposition, etch, magnetics, polymers, etc.
- Unmatched metrology tools and experience
SOURCE: Innovative Micro Technology